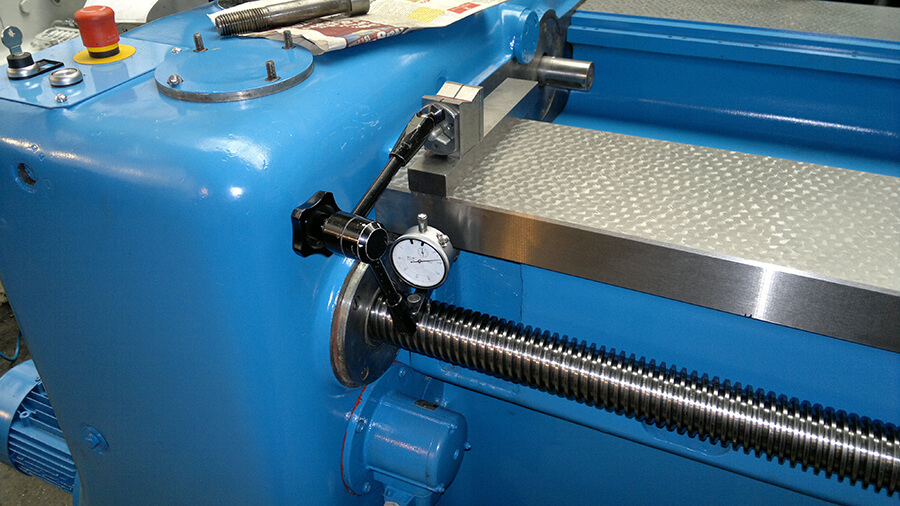
Specialized service
Your machine tools deserve only the best, and we bring you qualified tailored service.
With our team of experts, you can count on precise and efficient maintenance and repairs. Extend life and minimize downtime with our professional approach to machine tool service. Rely on us to keep your business moving with the optimal functionality of your devices.
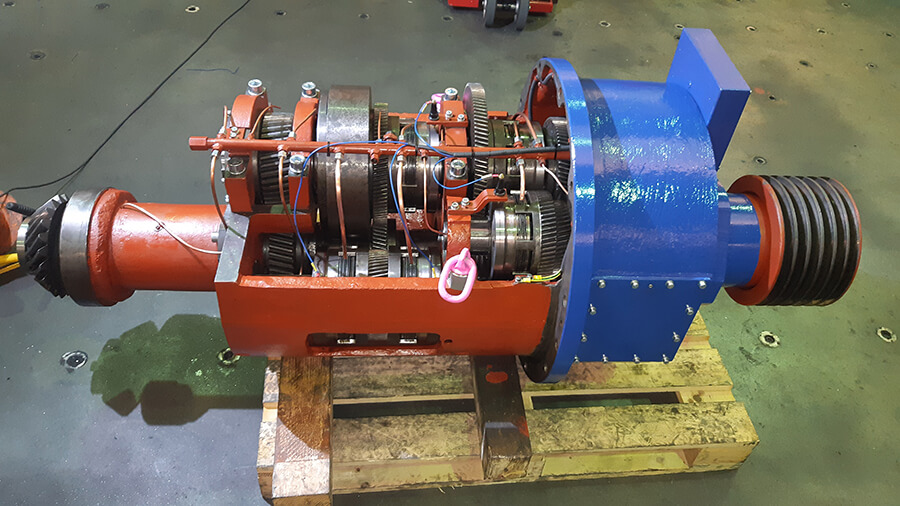
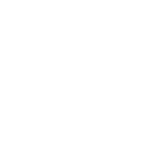
Quality
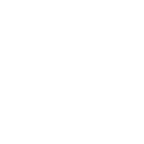
Reliability
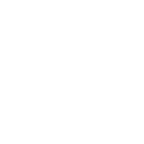
Precision
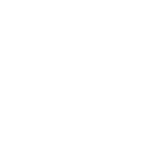
Flexibility
Specialized and qualified service of vertical lathes, rotary tables and other machines
Preventive maintenance
Preventive maintenance is the key to minimizing unexpected failures and maximizing the life of your machines. We offer proactive maintenance programs tailored to the specific needs of your high-performance vertical lathes. Our team performs regular inspections, lubrication and replacement of worn parts to keep your machines in optimal condition. By addressing potential problems before they escalate, we help you avoid costly downtime and maintain uninterrupted production.
Preventive machine tool service is key to maintaining optimal performance and extending the life of the machine. Here are some reasons why it is important to carry out preventive maintenance regularly:
Prevention of outages:
Regular servicing can spot potential problems and address them before anything serious happens. This reduces the risk of unexpected outages, which can lead to unplanned delays in production.
Performance Optimization:
Preventive maintenance involves checking, adjusting and setting the equipment to optimal performance. This improves the accuracy, speed and overall performance of machine tools.
Extending machine life:
Regular service can prevent wear and breakdowns, ultimately extending the life of the machine tool. This can be key to protecting the investment in more expensive equipment.
Reducing Repair Costs:
Repairs made during preventive maintenance can be less costly than repairs in the event of a major breakdown. Regular service can thus contribute to overall cost savings.
Work safety:
Thorough service can identify potential safety issues and ensure that the machine meets all safety standards. This protects not only the machine, but also the employees who work with it.
Optimization of energy consumption:
Properly maintained machine tools can be more energy efficient. Preventive service may include inspection and adjustments to help reduce energy consumption.
Overall, regular preventive service is an investment that pays off in the long run, ensuring reliable and efficient operation of machine tools.
Case Studies
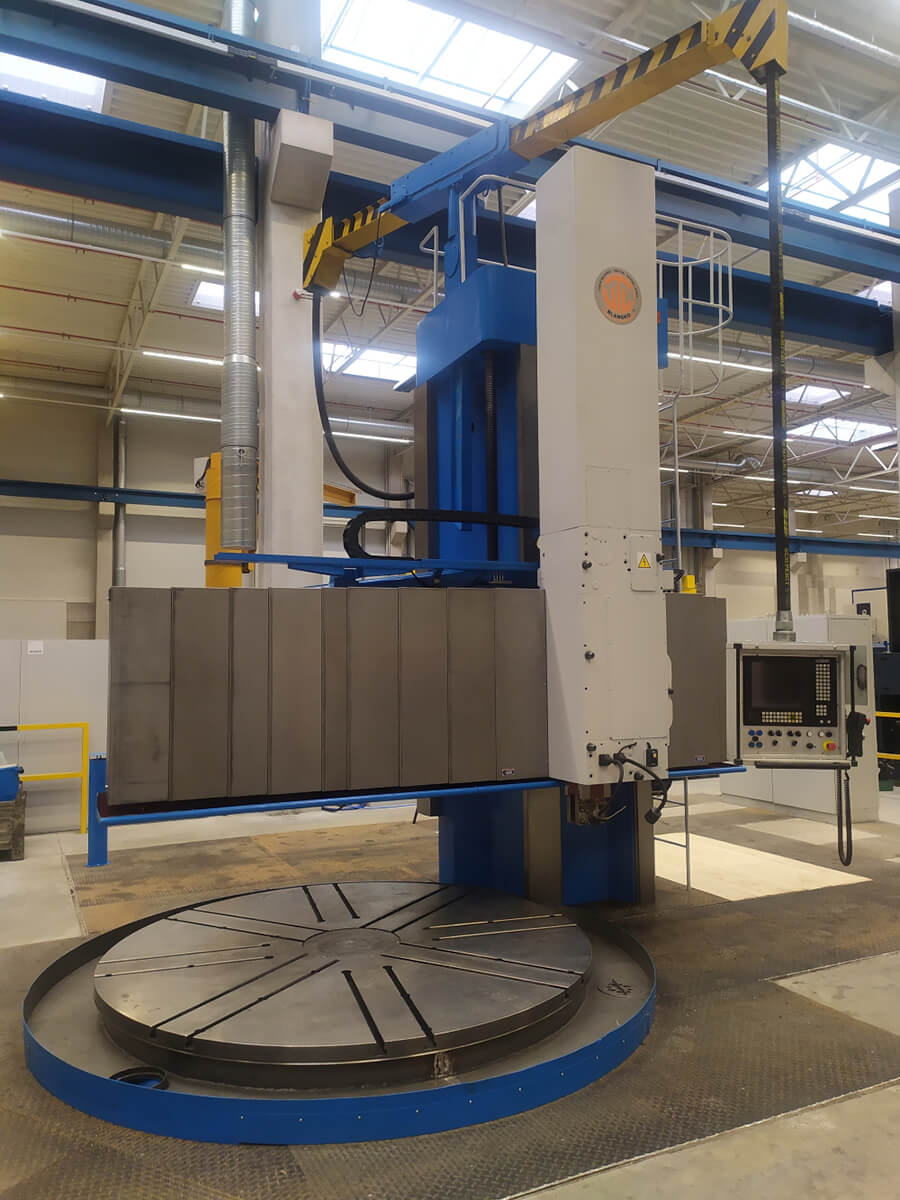
Howden ČKD Compressors s.r.o., Nehvizdy
Frequently Asked Questions
The frequency of service depends on the type of machine, its operating mode and the intensity of use. In general, regular preventive service at least once a year is recommended.
Decreased performance, unusual noise, vibration, imperfect machining results and recurring failures are signals that the machine requires service intervention.
Regular service usually includes inspection of all machine functions, verification of machine accuracy and calibration, inspection of electrical armaments, electronic systems, fluid systems, and a proposal to repair or replace worn parts.
Some maintenance tasks, such as cleaning or lubrication, can be done by yourself. However, more complex repairs and settings should be carried out by a qualified technician.
We recommend choosing a qualified technician with appropriate experience in the field. Try to find out about the reputation of the service company and consult with other users.
Yes, older machines can be upgraded by overhauling or upgrading, updating software, or replacing some components, which can improve their performance and capabilities.
Regular preventive service, adherence to maintenance recommendations and operator training can significantly minimize downtime and extend the life of the machine.
